BAND-IT Cable Harness and HVIL Connector Clamping Solutions
September 09.2022 | Joining Solutions
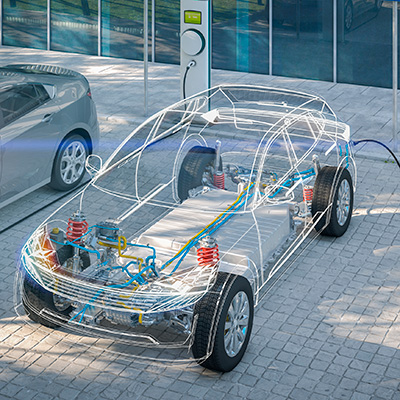
Today’s consumer hybrid and all-electric vehicles are assembled with more electrical cables than hoses and tubing found in previous generations of vehicles. Those high voltage cable systems utilize backshell connectors, EMI/RFI shielding, power distribution system components, and a variety of high voltage interconnection components to facilitate initial installation, but those components have to last the life of the vehicle. Many of the largest and most well-known cable harness manufacturers in the Hybrid and Electric Vehicle Industry trust BAND-IT Tie-Lok® ties to secure EMI sleeving and pluggable connectors they supply to the Tier 1 Automotive manufacturers.
BAND-IT products are proven to have a higher retained force, with lower profiles and less weight, while maintaining superior electrical continuity over other joining methods. This is especially true in harsh duty applications where vibration, corrosion, and effects of thermal cycling cause other solutions to fail. Since BAND-IT began serving the automotive HV cable market in 2007 we have supplied clamping solutions to Tier 1 to Tier 3 automotive customers for use in nearly all types of HV plug connectors for electromagnetic interference shield retention in these rugged applications.
Tie-Lok System Features
• Low-profile buckle and secure locking prevents shielding from being accidentally or inadvertently pulled away from the connector.
• One-size-fits-all solution provides reduced diameter clamps minimizing variation in the backshell connector design, reducing cost and the complexity of handling multiple part numbers.
• Tie-Lok metal bands are lower in weight and total cost versus other “customized” bolt clamps reducing weight and cost of the finished component.
• Metal band provides full circumferential electrical contact with the backshell of the connector, maximizing electrical performance and minimizing any system losses.
• Designed for high volume applications: Minimizes ergonomic and repetitive injury concerns with pneumatic installation tools and maximizes throughput at the assembly level.
• Robust Strength: Our clamping solutions are manufactured from Type 304SS for high strength and excellent corrosion resistance, other grades of stainless are available to meet OEM needs across the automotive industry